Why Site Diaries Fail
- John Lowry
- May 4, 2017
- 3 min read
Updated: Oct 18, 2022
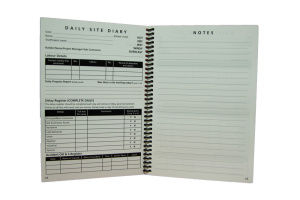
Until now, a daily site diary was the only way to record information at a construction site or workface remote from project and organisational management and administration.
Project information management systems are slowly taking hold for management to management (project and organisation), but site to management communications, apart from some inspection reports, is still substantially hand-written communication, aided by voice (phone) communications, email, text messaging and random photographs.
A Daily Site Diary is typically a large A4 format book, sometimes with a duplicate copy. It would be usual for site supervisor to complete the daily site diary, from memory, at the end of each day. Our research indicates that a site diary can have more than 200 fields to be considered or completed each day. The completed fields may generate more than 100 separate tasks or actions, per day, either in project or organisation management. It is typically supplemented by daily time sheets for each employee and a range of paperwork including site instructions, requests for information, delivery documents and records of oral instructions.
The information contained in the diary and supplementary site information is critical for contract management, variation management, program management, delay and extension of time management, payment entitlement, payment claims, progress and workforce management, payroll, accounting, workplace health and safety and other project and corporate functions.
To be effective, site diary and other site-generated data must be transferred to multiple systems on a daily basis. Completed data fields must be interpreted and tasks assigned to project and organisation management systems and people. it is all happening in a “pressure-cooker” environment focussed on meeting programme and contract deadlines. The contractual time to react to a diary entry can be between 2 and 5 days. The likelihood of getting diary data through an action process in this time is very low, if not zero.
Because of their nature, every field in a site diary must be considered, or at least sighted, by the completor and the receiver(s) every day, whether the field is filled or not.
Because the discipline of completing a site diary is tedious, and from memory, it is not uncommon for site diaries to be inaccurate and incomplete. The further time required each day to manually interpret the data and allocate tasks requires significant resources that are rarely, if ever, available.
We estimate that cost to a small to medium contractor / subcontractor of completing, analysing and acting on daily site diaries is a minimum of $140,000 per annum per job. The cost of NOT acting is much more.
Our research indicates that the interpretation and action of site diaries is the most likely point of breakdown in contract management.
The result is that much of the data contained in site diaries is archived before important tasks and functions are enacted, significantly increasing contract risk and reducing the ability to manage project and organisational issues at the earliest stage. It is not uncommon for site diaries to be manually “mined” for data well after the event to assist with proving a claim. Under most modern contractual time-bars, contractors will have foregone much of their contractual entitlement to make a claim.
Other management KPI's taken from, such as earned value analysis, are expensive and time consuming to compile. We estimate the average cost of an earned-value analysis for a medium-sized contractor or subcontractor is $7,000. It is unlikely that earned value analysis is performed on a reasonably regular basis in most organisations.
New data management technologies and methodologies are becoming available to significantly improve accuracy and productivity in relation to the flow of communications and data from construction sites through management systems. The next wave of innovation in data flow and data management will increase its potential many times over.
One of the great advantages with an integrated mobile diary is the ability to adopt ”just in time” principles and exception reporting, management innovations that have been adopted in manufacturing since the 1970’s. Line operators and supervisors are only required to report on issues as they arise. But when they are reported they will generate tasks that require action by others. Important information required for time-barred notices does not easily slip through the cracks. Add to this the ability to automatically fill information into project information management and corporate systems such as payroll, accounting and HR / WH&S systems and the productivity and accuracy gains multiply quickly. Tasks can be deployed direct from programming / scheduling programs and progress automatically monitored.
Management changes to leverage these technologies will multiply productivity gains.
We estimate that, apart from the improved risk profile and fast response times, intelligent mobile connected systems will save over 90% of transactions currently managed manually.
MIAC Workflow Integration is one such "business disruptor" platform that promises to slash the cost of data collection and management through automation of collection and dissemination of data.
The Author is a director of thepowertool pty ltd, developers of MIAC Workflow Automation.
Comentários